A K&S IConn ProCu PLUS ball bonder, supplied by Inseto, provides Alter Technology TÜV NORD UK with additional and enhanced manufacturing capabilities, empowers the company to take on new kinds of projects and promises a rapid return on investment.
Alter Technology TÜV NORD UK Ltd – formerly Optocap and based in Livingston, Scotland – provides contract package design and precision assembly services for a wide range of optoelectronic, microelectronic and MEMS devices.
Offering end-to-end backend semiconductor manufacturing, from wafer singulation to assembled product, the company’s design and process IP enables customers to reduce development and manufacturing costs plus reduce time to market.
Matt Booker, Head of Sales and Assembly Services, comments: “We serve a variety of high-tech markets. For example, we’ve done projects for ESA, the European Space Agency. We also have customers in medical and we’ve made components for machine vision systems in the industrial sector.”
Alter Technology UK recently attained AS/EN 9100 quality management certification, which is based on ISO 9001 but with a focus on the aviation, space and defence industries.
“We’re the only packaging company in the Alter group,” continues Booker, “and we serve worldwide markets from right here in the UK. Most of the work we do is for customers directly, but we also enable our parent company to take on projects that require off-the-shelf devices as well as custom-packaged chips, which is where we come in.”
Product volumes range from 10 devices through to a few tens of thousands.
Alter Technology UK operates a Class 10,000 cleanroom with specific areas therein achieving Class 1000. There is also a designated ‘grey area’ where activities such as wafer sawing, destructive testing and cross sectioning/polishing take place.
Equipment used in the company’s manufacturing processes includes wafer saws, pick and place machines, wire bonders, plastic mould injection and hermetic sealing equipment. Ancillary equipment includes a non-contact metrology system, an x-ray machine and a destructive test system which are all used to validate manufacturing processes.
The company also has a ball bonding machine, which was bought from new and has provided over 10 years of service.
A ball bonder is a type of wire bonding machine. It works by melting the tip of the wire to create a ball, which is then placed to make the first contact. The wire is then drawn to the second contact point. The advantage of a ball bonding process over a wedge bonding process is that the wire can be taken in any direction after the first bond, which leads to a much faster process.
In early 2019, Alter Technology UK decided to invest in a second and more capable ball bonder. Booker explains: “We recognized that our ball bonder was lacking features that prevented us from bidding on a few upcoming projects. A newer, more advanced machine would help us respond to RFQs and pursue new kinds of work. There’s also a benefit in having some equipment redundancy and having two machines than can do much of the same work, particularly seeing as our original ball bonder was running at near full capacity.”
Alter Technology UK turned to its long-time and trusted supplier Inseto for recommendations.
The Ideal Fit
Established in 1987 and ISO 9001:2015 certified since 2005, Inseto is a technical distributor of equipment and related materials to the semiconductor, microelectronic and advanced technology sectors.
Based in Andover, the company has three divisions. Its Equipment Division provides manufacturing equipment for the microelectronic, photonic, electronic, photovoltaic and semiconductor industries; its Consumables Division provides assembly materials and machine consumable items and its Adhesives Division provides technically advanced adhesives for bonding, sealing and encapsulation.
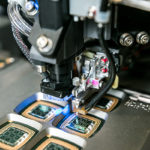
Figure 1
Inseto, whose relationship with Alter Technology UK (Optocap as was) dates back to the manufacturer’s earliest trading days, recommended a Kulicke&Soffa (K&S) IConn ProCu PLUS automatic ball bonder (see figure 1). Note: Inseto has been representing K&S in the UK, Ireland and the Nordic regions for more than 10 years, and one of Inseto’s directors used to work for K&S.
The IConn ProCu PLUS has an ultra-fine pitch (of 40microns) wire bonding capability for copper wire (of 15 to 30microns in diameter) and gold wire capabilities of 35microns pitch with 15microns diameter wire. Also, the bonder has an impressive looping capability of 7.6mm in length for 25microns diameter wire and 3mm in length for 15microns diameter wire. Ultra-low loops of 40microns high for 15microns diameter wire and 80microns high for 25microns diameter wire. Wire sway is 25microns @ 3 sigma for wire lengths shorter than 2.54mm and +/- 1% of wire length at 3 sigma for longer wires. The bonding area is 56 by 90mm (X and Y axes respectively) and total bond placement accuracy of 2microns at 3 sigma.
The ball bonder can also do stand-off stitch bonding, where a bump is placed on the die pad first then the wire bond is made from the package (where the ball is placed) to the bump on the die.
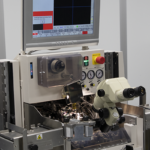
Figure 2
Installation (see figure 2) and training took place in Q3 2019 and the bonder was put to immediate and good use.
Stephen Robertson, Engineering Manager of Alter Technology UK, comments: “For one customer we’ve been manufacturing LED arrays that are about 1” square in size and have 96 LEDs each in relatively high volumes since mid-2016. The IConn ProCu PLUS can do the complete bonding for a chip – so that’s pattern recognition to find two fiducials on each of the 96 LEDs and make the 192 bonds at a rate of about six bonds per second – in less time our older machine takes to just perform the alignment.”
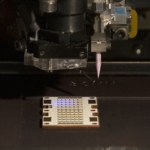
Figure 3
Figure 3 shows a 60 LED array being wire bonded at Alter Technology UK.
Robertson goes on to say that the biggest benefit of the new bonder is probably the machine’s ability to bond using 50micron wire. This is beneficial for high power applications where high current carrying capacity is required. Robertson says that since taking delivery of the IConn ProCu, Alter Technology UK has received several enquiries for bonding and packaging high current die, one of which is for a silicon carbide (SiC) Schottky diode for a space application that will be rated at 60A.
Another advantage of the K&S system is its ability to perform copper ball bonding. This is typically done as a cost reduction exercise for high volume products but Robertson, a member of the ESA Hybrid & Packaging Working Group, says that an increasing number of COTS components are bonded with copper, which is limiting options for high reliability space applications. “There are some background activities going on to evaluate copper bonding in space applications and having this capability may open up new opportunities in this area for us in the near future.”
Robertson is also impressed with the IConn’s automatic load capability, which is of great benefit on higher volume projects. In automatic mode, devices are placed on lead-frames (or strips) in a cassette on the input side of the bonder. These are drawn into the bonder and indexed through to the bonding area, where they are automatically aligned and bonded. The bonded strips are then fed into the output cassette.
Horses for Courses
“Our other ball-bonder is far from redundant though,” comments Booker. “Our operators are currently more familiar with it and write many programs each week that are for low volume work. The IConn ProCu PLUS is coming into its own on, for us, relatively high-volume projects, and we have about 10 programs for repeat orders. Over time, more operators will be trained on the new machine.”
Alter Technology UK predicts a quick return on investment. This will come through reduced manufacturing turnaround times, which in turn will enable the company to take on additional work, and doing projects requiring copper for space applications; which are typically high value.
Despite most operators being familiar with the older bonder, programming of the IConn ProCu PLUS is easier in Robertson’s opinion and more operators will be trained in the near future. This will enable small volume and custom work to be done on the new bonder and give Booker the ‘equipment redundancy’ he needs if the older bonder needs to go offline for any reason.
Robertson concludes: “Inseto and K&S have been extremely responsive throughout this entire engagement, from understanding our requirements and recommending a best-fit solution through to making sure we have the relevant training and continue to be happy with our investment. Inseto, in particular, is a key supplier to us. They’re our first point of contact and we trust their views.”
This article was written in close collaboration with Inseto (UK) Limited and appeared in the October 2020 issue of Commercial Micro Manufacturing and is online and is reproduced on our site with the editor’s kind permission here.